Non-destructive pulse high-voltage measurement of wiring
components to ensure insulation performance and improve the
reliability of electric vehicles (EVs).
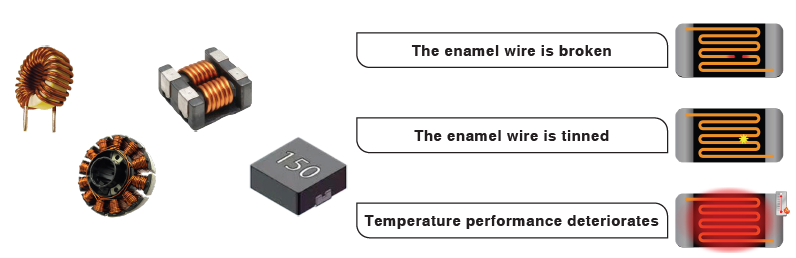
To enhance the electrical safety of electric vehicles (EVs), it is crucial to focus on the insulation performance of wiring components in the three electrical systems, such as motors, inductors, and transformers. While component manufacturers typically use withstand voltage testers to check the voltage withstand capability and insulation capacity, they often overlook issues caused by inter-turn short circuits in enamelled wires.
Withstand voltage testers, although they apply high testing voltages, operate at a frequency of 50/60Hz. When applied to the coil of the device under test, it creates a short-circuit condition, making it unable to detect inter-turn short circuit faults.
Furthermore, general LCR meters, due to their low measuring voltage, cannot easily identify significant abnormalities based on resistance, capacitance, and inductance values. Non-destructive pulse high-voltage testing techniques are necessary to detect inter-turn short circuit faults. By analysing the waveform, it becomes possible to observe subtle discharge phenomena caused by inter-turn short circuits and detect faulty components, thereby ensuring the reliability of wiring elements.
During the process of wiring, including wire routing, insertion, organization, bundling, handling, and assembly of components, improper handling by personnel can result in damage to the insulation of the wire-wound components. This can lead to defects such as complete or partial short circuits between the same winding or between different windings. These faulty wiring components may experience corona discharge or spark discharge, weakening their insulation capability and reducing the reliability of the electric vehicle system. Over time, the accumulation of moisture and dust in pinholes or cracks of the wire insulation may cause motor or transformer failures. In severe cases, it can lead to burning and affect driving safety.
In simple terms, when a portion of the motor winding is short-circuited, it prevents the induction effect. This leads to an asymmetrical magnetic field, causing the remaining coils to experience higher current. As a result, the motor exhibits increased vibrations, higher current, and a relative decrease in output power. Over time, this can lead to noise, overheating, and even motor burnout
To meet the requirements of high and low volume wiring component pulse testing, the optimal choice for automated production is high-speed testing at 10 times per second.
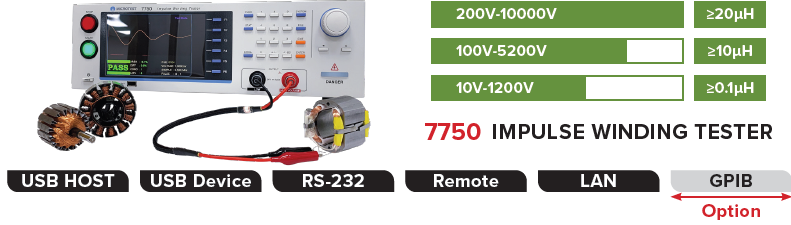
The MICROTEST 7750 Interlayer Short Circuit Tester is designed for reliable insulation quality testing of high- and low-winding components. It utilizes non-destructive pulse voltage for waveform sampling and comparison, effectively detecting insulation issues in motors, transformers, BL inductors, and other components.
It supports pulse voltage outputs of 1200V, 5200V, and 10000V respectively, and employs 200MHz high-speed sampling technology to analyse subtle discharge faults. It offers six analysis and comparison modes, including total area comparison, area difference comparison, corona number comparison, jitter number comparison, second derivative comparison, and waveform comparison mode. With a testing speed of up to 10 times per second, it is the optimal choice for automatic production lines of winding components.
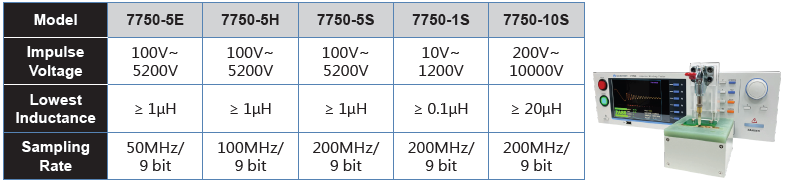
The 7750 utilizes non-destructive high-voltage, high-speed pulse measurement technology.
The 200MHz high-speed sampling captures dampened waveform, effectively detecting coil short circuit and insulation defects.
By applying a pulse voltage to the terminals of the winding coil, a damped oscillation waveform is generated through L/C resonance without damaging the test object. This allows for the comparison of instantaneous waveforms between a standard reference and the test object, enabling the early detection of faults such as interturn short circuits, internal coil defects, or insulation flaws in the magnetic core. This method ensures the quality and longevity of the product.
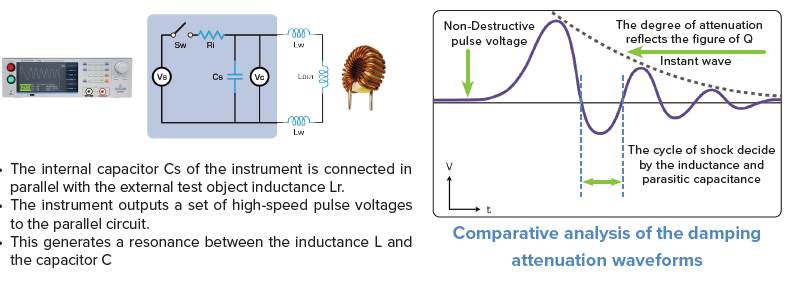
The 7750 interlayer short circuit tester ensures reliable testing of
wound components by detecting issues like electrode welding,
short circuits between winding layers, and inadequate insulation of magnetic cores.
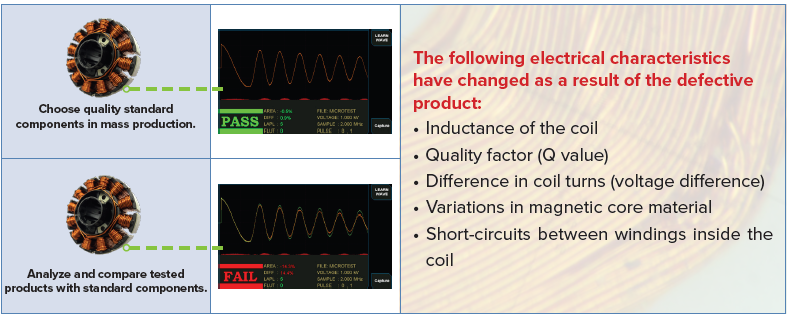
As a specialist distributor, Telonic Instruments provides a comprehensive range of test instruments and programmable AC and DC power supplies from leading manufacturers, including Kikusui, Delta Elektronika, Lab-Power, Rigol, Siglent, Brymen, Danisense, Tekbox, Graphtec, Sensepeek, Microtest, JBC, and Micsig.
With over 50 years of experience, Telonic, based in Wokingham, Berkshire, has been a trusted partner in supporting the electronics, automotive, aerospace, education, manufacturing, and research and development sectors across the UK. Our commitment extends beyond sales to include service, calibration, and equipment hire, ensuring our clients have the resources they need to succeed.